An articulated robot is one that has rotary joints. A rotary joint is a relationship in the middle of two objects. The relationship allows both objects, even though each is connected to an additional one object, the ability to rotate or have movement up to 360 degrees. Most of the time these two objects that are connected together are cylindrical. The relationship gives both objects increased capabilities to accomplish work functions. Articulated robotics usually have several of these connections which gives them a great deal of flexibility in performing work duties.
Each joint that a robotic has represents an growth in free time to accomplish tasks. There is no limit to the estimate of rotary joints that articulated robotics can have and a robotic may have other types of joints to growth its ability even more.. After a sure estimate of joints, however, there would be diminishing ability of the robotic to do any efficient work. All the movements of each of the objects that are connected together to originate articulated robotics must be programmed to move in order to do the tasks that they are assigned to do.
The more joints that a robotic has, the more involved become the robotic functions. An growth in the complexity of the robotic would growth the set of instructions that tell the robot when, where, and how to move. usually articulated robotics are assigned a miniature estimate of tasks to perform.
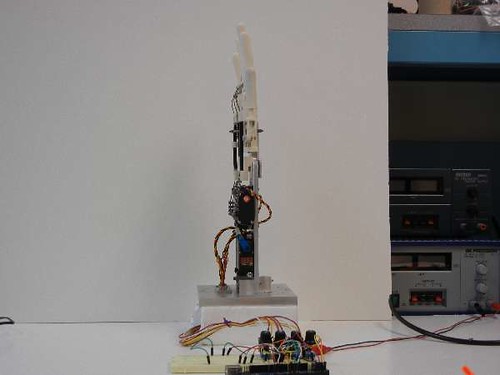
Most of the time articulated robotics are assigned to one work station in a group of work stations that accomplish individual steps in manufacturing or assembly operations. To originate the work assignment for an articulated robotic work station one must take into inventory the:
- How much weight is required to be lifted to complete this task?
- How much time is required to complete the task?
- What movements are require to complete the task?
- What position or positions are required to complete the task?
- How does the environment follow the completion of the task?
- How does the task follow the environment where the task is accomplished?
Not unlike the industrial engineering functions in factories of years gone by, the agenda designed to run a robotic work station must take into inventory how it interacts with the other work stations on "the line". One of the big differences in the middle of the work increments defined by industrial engineers years ago and the agenda steps defined by robotic programmers today is the inaccuracy of humans as opposed to the speed and accuracy of robotics. Articulated robotics are capable of very correct and unending, repetitive tasks that naturally cannot be done as accurately and as speedily by humans. In many cases the robotic transfer for a human in a output line can accomplish many more steps in the manufacturing process than the human could ever hope to accomplish at the same work station.
The joints of articulated robotics are programmed to work in unison with other parts of the robotic or can work independently. This characteristic gives the robotic a high degree of functionality. There are great variations in the kinematics of articulated robotics. This arrangement of the rigid member and the joints in the robot determines what the type and range of motions of the robotic. Simple tasks that are to be performed require only a miniature estimate of rigid parts and joints, while many rigid parts and many joint can do more tantalizing tasks or even several tasks.
The utility of articulated robotics has grown so much in the last few years that they can now do the most miniature work on the smallest objects, while their counterparts work with very large objects.
Characteristics of articulating robotics have moved toward meeting the needs of demanding manufacturing operations. Directly coupled drives are much more dependable than robotics built with belts, pulleys or chains. There are varied mounting options, depending on robotic size, upright, inverted, or wall, anything meets the needs of the application. Cables are enclosed in the body of the housing to eliminate entanglement. Encoders have absolute positioning so that homing or calibration is eliminated at power-up.
Other units have both pneumatic and electrical connections. With articulated robotics installed on a rail more than one unit can share the same central processing unit. These units are most versatile for medium payloads and work well for welding, wash down and clean room applications.
Small articulated robotics, if installed on the floor, require less floor space for operation. These type units can be configured in many ways to adapt a wide range of reach, payload, and application requirements. Some units are controlled by multitasking controllers with individual axis monitoring. A particular electric gripper or two pneumatic grippers can deal with components. The gripper force is continuously adjustable, so that brittle items are handled safely and securely.
Larger counterparts of these robots have extra long reach area with very small footprints, but with higher payloads. These are useful in spot welding, material handling, sealing, die and speculation casting, material movement, machine tending, assembling of small parts, calibration, and testing, grinding, polishing, and bonding
Larger models of articulated robotics are designed without the need for counter-balancing. These units have advanced link structuring and have the ability to deal with very heavy payloads, usually this type of robotics has mechanical stops and limit switches to originate a safe working environment. These robots are used to deal with engines, handling car bodies, tantalizing large appliances, speculation casting, and forging applications. Some models are built to withstand extremely cold temperatures with the need of heating or shrouds. These are the real work horses of industry.
Articulated Robotics - Robots That Move and Do Work